Handgun Cartridge Crimping
Judging by the volume of questions I've been receiving about the subject, the crimping process for handgun cartridges continues to confuse people that are new to reloading. In this article, I'll try to clarify things.
In reloading terms, the crimp is an operation performed by a die on the mouth of the case. Sometimes the crimp is applied to provide additional 'hold' between the case and the bullet. Other times, it can simply be an operation that removes the belling on a straight-walled case to allow it to chamber freely. Cartridges can be crimped using a dedicated crimping die as an additional operation, or a crimp can be applied with a combination seating/crimping die as the bullet is seated. All handgun cartridges require some sort of crimp.
There are two types of crimp used when reloading handgun cartridges: the roll crimp and the taper crimp.
Roll Crimping
With a roll crimp, the diameter at the very end of the case mouth is reduced, and rolled inward toward the bullet, leaving a slight radius
at the top of the case. Since the case mouth is 'embedded' into the side of the bullet, the bullet itself must be of a design
capable of accepting a roll crimp; in other words, the bullet must feature some place for the crimp to go. Cast lead bullets
designed for a roll crimp feature a crimp groove, into which the case mouth is rolled during the crimping process. Jacketed
bullets have a feature called a cannelure. A cannelure is a row of small vertical 'fins' embossed into the jacket around the
circumference of the bullet. The purpose of the cannelure is to provide a place for the case mouth to grip the bullet - that
will not deform the bullets or allow the case mouth to cut through the jacket. During crimping, the case mouth flattens out the
small fins when it is rolled into the bullet.
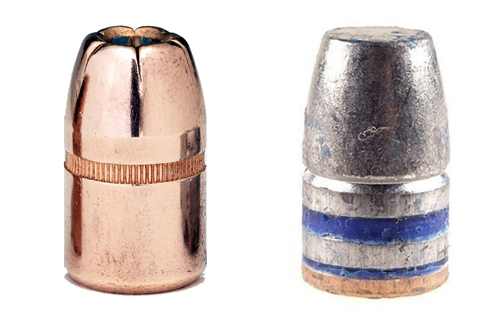
A roll crimp should not be applied to any cast lead bullet that does not have a crimp groove, or any plated or jacketed bullet without a cannelure. At the very least you will experience reduced accuracy due to a deformed bullet; at worst you'll cut through the plating or bullet jacket, which can strip off when fired and wind up in the barrel or forcing cone. No good can come of that.
Since a roll crimp provides extra hold between the bullet and the case, it should be used in applications where bullet pull is likely. The term 'bullet pull' describes a condition where the bullet in a loaded cartridge works its way out of the case during recoil. This usually occurs in magnum revolvers, or very lightweight revolvers that fire non-magnum cartridges. Under recoil, the sudden backward acceleration of the revolver causes the bullets in the rounds remaining in the cylinder to pull out of the case slightly; and each shot causes more pull. This results in inconsistent ignition, and can even can cause the revolver to lock up after a few shots if a bullet protrudes out the front of the cylinder far enough to contact the frame.
When slower burning powders are used, a strong roll crimp can produce more consistent powder ignition and velocity. The additional hold provided by a roll crimp can keep the bullet in place in the case a tiny fraction of a second longer, which results in a more consistent burn. Magnum revolver cartridges loaded with powders like H110, W296, IMR 4227, or Hodgdon Lil' Gun perform better with a strong roll crimp (this is often mentioned in the reloading manual as well).
When Should a Roll Crimp Be Used?
A roll crimp can be used on any cartridge that headspaces on the rim, belt, or shoulder, when it is loaded with the appropriate
bullet (see above). A different type of crimp is needed when the cartridge headspaces on the case mouth, or when a
bullet without a cannelure or crimp groove is used.
Taper Crimping
Unlike a roll crimp, a taper crimp does not leave a radiused edge on the case mouth. A taper crimp simply flattens
out the 'belling' that was previously done by the expander die, and squeezes the case mouth tightly against (but still
mostly parallel to) the sides of the bullet. A taper crimp leaves a distinct 'step' at the top edge of the case mouth.
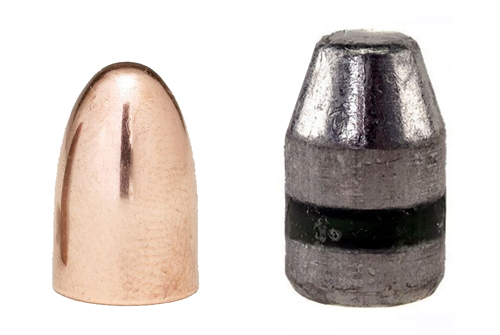
When Should a Taper Crimp Be Used?
A taper crimp should be used for any rimless straight-walled or tapered case (like the 9mm, .40 S&W, .45 ACP, etc) because
these cartridges headspace on the case mouth. If a roll crimp is used on any of these (or other rimless straight-walled
cartridges), the round will not properly headspace in the chamber. Instead, it will likely headspace on the extractor.
If conditions are just right - or wrong depending on how you look at it - a cartridge of this type with either a roll crimp
or too much taper crimp can fire with the case mouth pushed into the rifling. This will cause an extreme pressure
spike which can result in catastrophic failure of the cartridge case and the firearm.
Note that there is no reason why you can't apply a taper crimp to a bullet with a cannelure or crimp groove, however, the bullet does not need to have either of these features in order for a taper crimp to be used.
Crimping Dies
In three-die pistol sets, the seating die does double duty as the crimping die. The seating stem in the die
seats the bullet, and the die body itself has an internal contour that will produce a crimp on the case mouth.
Therefore, the height of the seating stem controls the bullet seating depth (and cartridge overall length), while the
height of the die body in the press controls the amount of crimp. Combination seating/crimping dies are available
that will produce a taper crimp only, a roll crimp only, or either type of crimp depending on the height of the die
body in the press. Dies of the latter type will produce a taper crimp when the inside of the die body first
contacts the case mouth; and will leave a roll crimp if the die is set deeper in the press.
There are dedicated crimping dies available for sale by themselves, or as part of a 4-die pistol set. If a separate crimp die is used, the combination seating/crimping die should be set up only to seat the bullet by backing off the die body a turn or two so that it does not touch the case mouth during the seating process.
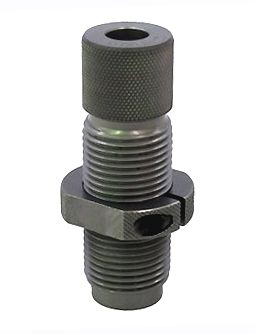
Many reloaders that use cast lead bullets for semi-auto pistols prefer a separate taper crimp die. The reason is that a combination seating/crimping die crimps the cartridge during the seating process, while the bullet is still moving. This can result in a small raised 'ridge' of lead at the case mouth that can affect the way the cartridge chambers/headspaces. Separating the seating and crimping operations prevents this ridge from forming.
Setting Up The Crimping Die
Here is an easy way to set up a combination seating/crimping die:
- Take the die out of the press.
- Place a sized and belled (but not primed and charged) case into the shell holder, and run the ram all the way up.
- Remove the seating stem from the die and screw the die body into the press until you feel the die contact the top of the
case, then back it OFF one full turn. Run the empty case up and down to verify that the die does not contact the case
mouth, and temporarily lock the die in place.
- Place a bullet onto the empty case, re-install the seating stem into the die, and gradually seat the bullet until you
achieve the desired cartridge overall length.
- Remove the dummy round from the shell holder and put it aside.
- Back the seating stem way out (or take it out).
- Put a round of factory ammo into the shell holder and run the ram all the way up.
- Loosen the locking nut on the die and screw the die body into the press until the die touches the factory round.
The crimp shoulder inside the die body is now touching the top of the factory crimp.
- Lower the press's ram to back the factory round out.
- If the press cams over at the top of the stroke (like an L-N-L single stage), back the die off 1/4 of a turn.
If the press does not cam over at top (like a Rockchucker or most progressives), screw the die in an additional 1/4 turn.
- Lock the die in place.
- Remove the factory round, and run your dummy round back up into the die. Reinstall the seating stem and turn it until it touches the top of the bullet. Remove your dummy round and inspect the crimp.
This will get the crimp very close. Adjust as needed, but you should never have to turn the die more than 1/2 turn in either direction from this point onward. If you do, you're doing it wrong. Keep the dummy round you made to use as a gage to aide future setups when you load the same bullets again. For a dedicated crimping die, perform steps 6-11 above, using a factory round as a gage to get the crimp close.
Verifying Proper Crimp
The most valuable tool to help you to verify that you have the right amount of crimp is a cartridge gage.
A cartridge gage is a cylinder of steel with a very tight version of your gun's chamber in it. To use the
gage, simply drop the finished cartridge into the opening. If it fits in the gage, it will fit in your chamber.
These gages are caliber-specific, and allow you to quickly check the cartridge's overall length, diameter, and case length.
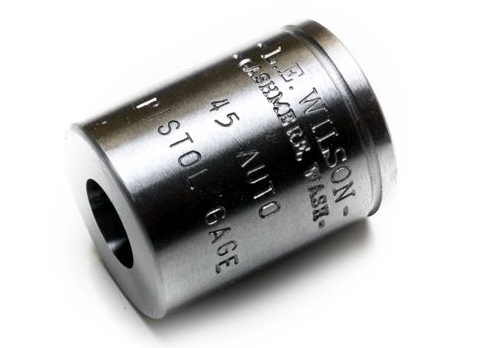
If you haven't crimped enough to fully remove the belling, the cartridge will not gage. If the cartridge won't gage, it might not chamber. Also, if you over-crimp, it is possible to bulge the case just below the mouth to the point where the cartridge is out of spec. A case gage will also detect this condition.
A final step to verify that you're not over taper crimping is to make up a dummy round, and pull the bullet. Inspect the pulled bullet for any deformation where the case mouth was previously located. An obvious dent or ridge around the circumference of the pulled bullet can indicate excessive crimp.