Rifle Cartridge Neck Sizing
This is the last installment in a series of articles on case sizing. This time, we'll cover neck sizing of bottleneck rifle cases.
When a bottle neck case is fired, it briefly expands to fill the entire chamber, then contracts slightly when the pressure generated by the burning powder dissipates, allowing the case to be extracted from the rifle. If you wanted, you could take that freshly fired case and re-insert it into the rifle's chamber. Not only would it fit, but it would be an exact fit to your rifle because it was fire formed in the shape of the chamber. If you wanted to reload this case to be fired again in the same rifle, all you really would have to do is clean it up, and reduce the diameter of the case neck enough for it to hold a bullet again - leaving the case shoulder and body in the as-fired condition. This process is called neck sizing.
When Neck Sizing Is Appropriate
Cartridges for a bolt action or single-shot rifles can be neck sized. Since the case has been fire-formed to a specific chamber, a neck sized
cartridge can only be used in the rifle that last fired it. If your ammo is to be used in more than one rifle, full-length size it instead.
Cartridges for semi-auto, and lever or slide-action rifles should not be neck sized because the cartridge-to-chamber fit is too tight for reliable feeding.
Cartridges for these types of rifles should be full-length sized only.
Neck Sizing Dies
Neck sizing is best accomplished with a neck sizing die. This die is similar to a standard full-length sizing die except that the only part of the
die that contacts the brass is the portion that resizes the neck. The part of the die that would normally size the body and shoulder of the case
is oversized so that it will not form those parts of the case.
Like a full-length die, the neck sizing die has a combination expander ball/decapping pin. The expander ball in a neck sizing die performs the same function as the one in a full-length sizing die: The body of the die intentionally undersizes the neck, while expander ball enlarges it from the inside as it's pulled out of the case. his allows the die to provide a consistent inside neck diameter regardless of the thickness of the brass. Unfortunately, repeatedly undersizing and expanding the neck can make it brittle due to work hardening. Fortunately, there's another kind of neck sizing die called a bushing neck sizing die that can minimize work hardening.
A bushing neck sizing die (see Figure 1) features a separate replaceable bushing inside the die that controls the amount that the neck is sized. Bushings are available in various diameters, allowing you to select one that will squeeze down the neck only enough to hold the bullet (ideally, 0.002" smaller than the bullet diameter). The downside of using a neck bushing die is that multiple bushings are required for different case thicknesses. In other words, when you change headstamps, you will have to change the bushing if one of the manufacturer's brass is thicker or thinner than the other.
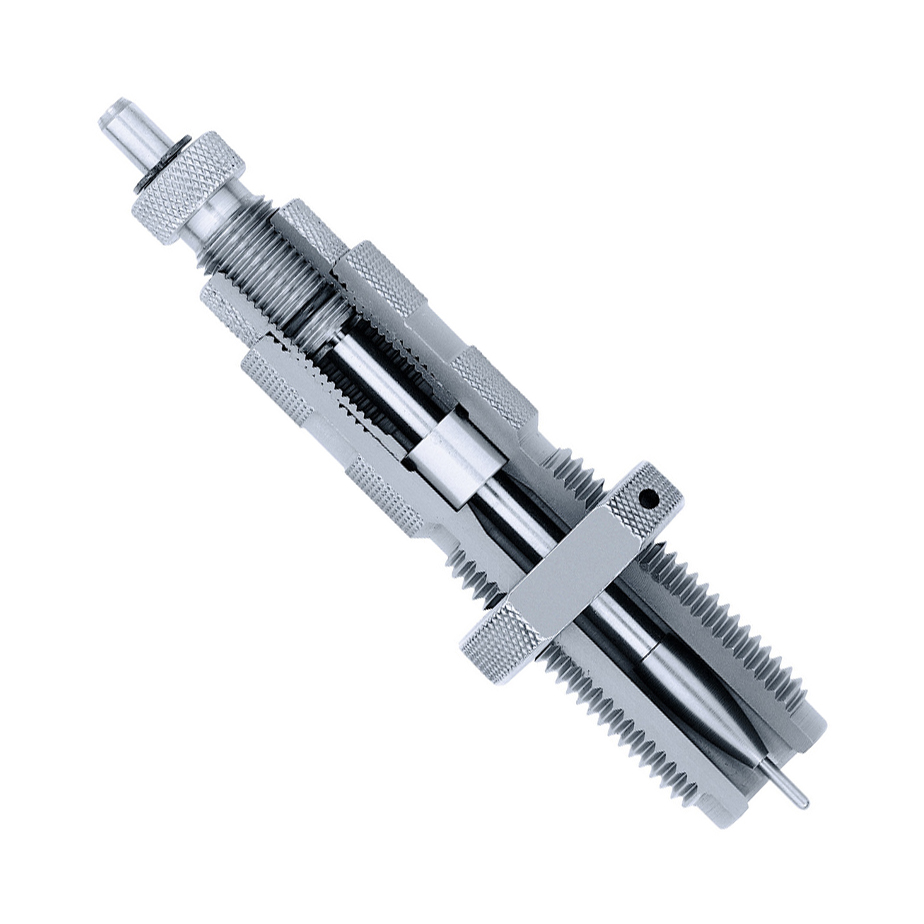
Partial Neck Resizing
There's a practice mentioned in many reloading books (including the NRA Guide To Reloading) called "partial neck resizing". This is accomplished
using a regular full-length sizing die that is backed off so that the case shoulder remains untouched during the sizing process. The theory behind
this is that a conventional full-length sizing die can be used to resize the neck, while leaving the shoulder and body of the case sized to match the
chamber. Don't do it.
If partial neck sizing was effective, the reloading equipment manufacturers wouldn't have to make dedicated neck sizing dies. The problem with partial neck sizing is that even though the die is backed off to miss the shoulder, the body of the die will still resize the body of the case. This causes the shoulder to bulge upward, which actually makes the cartridge headspace length longer. Since the cartridge starts out at the full length of the chamber, partial neck resizing makes the cartridge headspace length too long for the chamber.
I tried this once with a batch of 7mm Remington Magnum brass for a Thompson Center single-shot rifle, and not one of the resulting cartridges would chamber. You may be able to get partial neck sized rounds to chamber in a bolt action rifle, but if the cartridges are too long, the bolt will be hard to close, and hard bolt closure will cause the lubricant to be forced away from the bolt lugs. This can cause galling and premature wear on the rifle. Partial neck sizing is a bad idea.
There's a practical limit for even properly neck-sized cases. After 5 or so reloads, the cases will expand enough to make chambering difficult. When this happens, you should full-length size the cases and start the process over again.
Advantages of neck sizing
There are several advantages to neck sizing including longer brass life (more reloads before you have to scrap the cases), fewer reloading steps, and
less trimming of the brass.
If the failure mode for your full-length sized cases is either splitting, or thinning of the case above the web, you will see much longer brass life if you switch to neck-sizing (especially if you use a bushing die). Cracks and splits occur when the brass case has been work hardened to the point where the metal becomes so brittle that it cracks during firing, resizing, or bullet seating. Neck sizing works the brass less than full-length sizing, and a bushing neck sizer die works the case necks as little as possible. This results in less work hardening, and more reloads without splits.
When you full-length size, the case's shoulder is pushed back during the process. When the full-length sized cartridge is fired, the shoulder "blows out" to the size of the chamber, causing the case to stretch. The case does not stretch evenly along its full length. Instead, most of the stretching occurs in the case walls just ahead of the web (see Figure 2), which causes the case to become thinner in this area. Too much thinning can result in a full or partial case head separation (the worst kind of failure). This thinning will often appear on the outside of the case as a bright ring, bulge, or crack just ahead of the rim of the case.
When you neck size, very little case stretching occurs, so the case walls do not thin out. Also, since there is less case stretch, you will not have to trim as frequently (or at all) when you neck size. Another benefit of neck sizing (with a neck sizing die) is that you do not have to lube the cases prior to resizing them. This eliminates two reloading steps: Lubing the cases, and removing the lube after sizing.
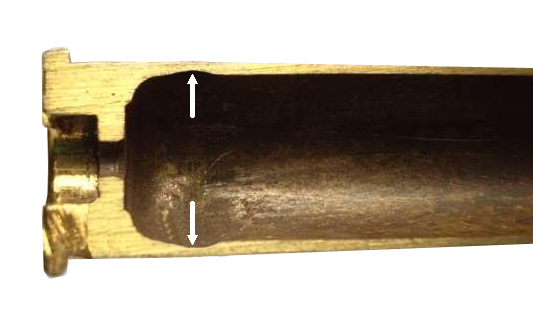
Disadvantages of neck sizing
As stated earlier, you cannot use neck-sized ammo in any firearm other than the rifle that last fired the case. If you have several rifles of the
same caliber, you have to take care to keep the neck sized ammo clearly marked as to which rifle can fire it, and keep it separated from the cartridges
of the same caliber that are full length or neck sized for a different rifle.
You may also find that your neck sized ammo produces larger groups than identically loaded full-length sized ammo. If this is the case, it is likely caused by something being non-concentric. Looking down the bore of your rifle from the breach, your rifle's chamber (and the ammo you fire in it) consists of a series of lined-up circles. There's a large "circle" in the chamber where the body of the cartridge goes, another one for the shoulder, another for the neck of the cartridge, as well as smaller circles that make up the leade (the unrifled portion of the chamber with the same diameter as the bullet) and the rifling itself. In a perfect chamber and barrel, all of these circles would be perfectly round, and would ‘line up' so that a line through their centers would be perfectly straight and centered in the bore. Unfortunately, there is no such thing as a "perfect" chamber and barrel. Even a carefully machined chamber and barrel will have some (maybe barely measurable) non-concentricity, and some rifles are much worse than others.
Even if you were in possession of a one-in-a-million concentric barrel, you still have to worry about the ammo. The same "circles" that are supposed to line up in the chamber exist on the ammo that you will be firing. The rim must be concentric with the body, which has to be concentric with the shoulder which should be concentric with the neck. In addition, any brass thickness variation within the case itself affects concentricity, as does the bullet seating angle. Of all of these factors, the bullet seating angle probably contributes the most to non-concentricity - especially if you're not using a competition seating die.
A full-length sized cartridge has a slightly looser fit in the chamber than a neck-sized cartridge. This extra clearance exists everywhere except for the fit between the outside diameter of the bullet and the inside diameter of the leade. By having clearance everywhere else on the cartridge, the bullet entering the leade can self-center, acting as a pilot to align the rest of the cartridge with the center of the bore.
With a neck-sized cartridge, very little clearance exists between the case and the chamber, which minimizes the ability of the bullet to center itself in the leade. If enough non-concentricity exists, the bullet can be shoved hard against one side of the leade when the cartridge is chambered, resulting in reduced accuracy.