Are Your Sizing Dies Overworking Your Rifle Brass?
I was resizing a batch of .223 cases that consisted of about 80% British military brass (RORG 89 headstamp) and 20% Federal brass (FC 12 headstamp). I was using an RCBS standard (as opposed to small base) full length sizing die. As I was working, I realized that that by feel alone I could sort the cases by headstamp with 100% accuracy. The difference in feel was not so much evident when the case was pushed into the die, but was quite obvious when the case was being removed from the die - while the expander ball was being drawn back through the case neck. The RORG 89 brass required a much harder lift to get the expander ball through the neck.
Why?
The first step in finding out "why" is to take some measurements. It would stand to reason that cases made by different manufacturers might have different case wall thicknesses, and that is indeed what we have here (See Figure 1). The FC 12 brass is 0.010" thick, and the RORG is 0.0135" thick. To understand why this has an effect on the force required to extract the case from the die, it's important to review the role of the expander ball in full-length resizing dies.

The Expander Ball
When you extract a bottleneck case from a full-length resizing die, you will first feel resistance as the case initially frees itself from the die. As you further raise the handle to lower the ram, you will feel almost no resistance for the next inch or two of ram travel, followed by a noticeable period of additional resistance just as the case is fully extracted from the die. This final bit of resistance is caused by the expander ball being pulled through the case neck. This is where the difference between the RORG and the FC 12 brass was very obvious.
The expander ball is necessary to ensure that your case necks all have a consistent inside diameter after resizing - regardless of the thickness of the case.
When a cartridge is fired, the entire case - including the neck - expands. The resizing die needs to reduce the diameter of the neck to the point where it will once again hold a bullet with the proper amount of tension. Since cases from different manufacturers vary in wall thickness, the reloading equipment makers design their dies so that the portion of the sizing die that reduces the diameter of the neck is small enough to reduce even the thinnest-walled cases so that the neck ID will be 0.002"-0.003" smaller than the bullet diameter. As a result, the die will make the neck of any thicker case much smaller than it needs to be, which is why it is necessary to employ an expander ball to increase the neck ID to the proper diameter.
You read that right: First the die makes the neck ID too small, and then it expands it back to where it should be. Ideally, the neck would only be slightly undersized so that the expander ball barely touches it on the way out. That was clearly NOT the case with the RORG brass and the RCBS sizing die that I was using.
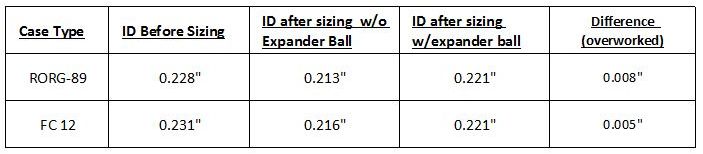
To figure out just how much the case necks were being over-worked, I measured the case neck inside diameters of the two headstamps before resizing, after resizing with the expander ball removed, and after resizing with the expander ball in place. The results are shown in Table 1.
It's clear that my resizing die is overworking both types of cases, but especially the thicker RORG-89 brass. Overworking the brass in this way can result in neck misalignment and/or excessive bullet run out (both of which will adversely affect accuracy), and premature case failure due to neck splits because over-worked brass becomes brittle due to work hardening.
Is it the same for all manufacturers of dies?
I wondered if simply changing the brand of die would fix the problem. So I purchased several manufacturers' full-length .223 resizing dies to try out. The results are shown in Table 2.
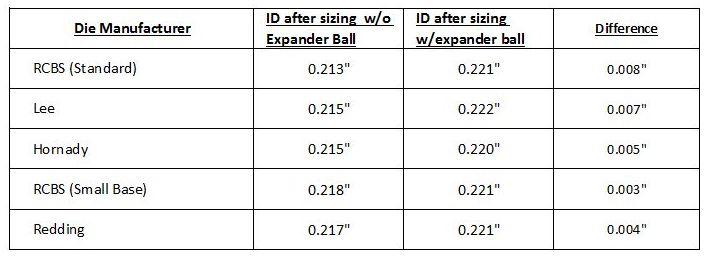
Some dies seem to be better than others, with the RCBS Small Base X die and Redding dies leading the pack. By "leading" I mean that they only overwork each case neck by 0.003" or 0.004". So, it appears that simply changing brands of dies will not completely alleviate the problem. What else can we try?
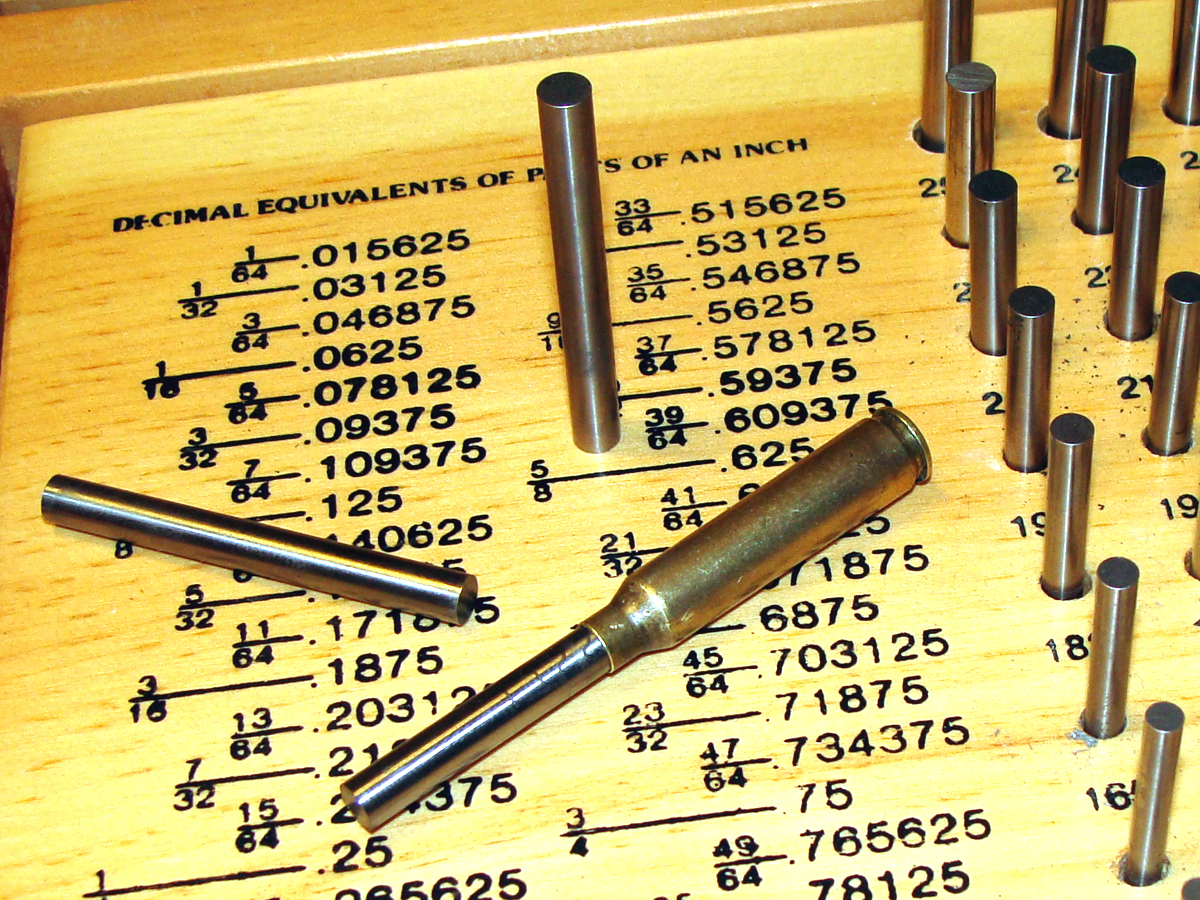
Use Bushing Resizing Dies
Manufacturers have realized this shortcoming of full length sizing dies, and have developed a type of die called a bushing sizing die. A full-length bushing sizing die features a replaceable insert (the bushing) that sizes the neck (see Figure 3). The manufacturer offers a series of bushings for each die to accommodate a range of case wall thickness. To select a bushing, you load a sample round, measure the finished outside diameter (at the neck) and select a bushing that is 0.002" smaller than your finished sample.
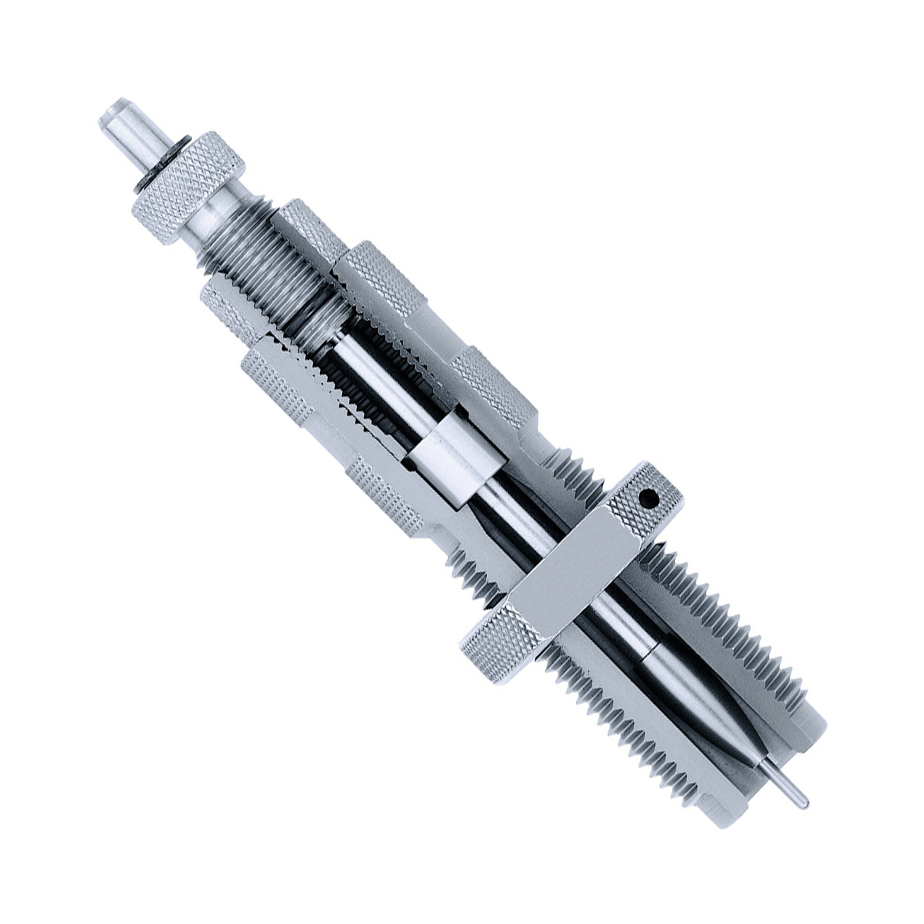
Using a bushing die will force you to pre-sort all of your cases by headstamp before sizing to ensure that your selected bushing will provide the proper neck tension. In my example, I would require one bushing for the RORG brass, and a slightly smaller bushing for the FC 12 brass. The bushing dies are equipped with an expander ball that shouldn't do very much expanding if the correct bushing is used, however it is needed to remove minor dents in the case mouths.
Bushing dies are available for commonly loaded calibers. Manufacturers generally do not make bushing dies for unusual calibers. Unfortunately, "unusual" calibers are generally the ones that require the use of expensive brass that you want to avoid over-working.
Hone the Inside of the Die
If you cannot find a bushing die for the caliber you are loading, you can hone or lap the inside of a standard sizing die to minimize the amount that your cases are over-worked.
Modifying a die makes the most sense if you have a large quantity of brass from a single manufacturer. If you have mixed brass, you can still benefit from modifying your die because standard resizing dies tend to overwork even the thinnest cases. To determine the proper final dimension for the neck portion of your die, repeat the process described above for selecting a bushing. If you have mixed headstamp brass, use the finished outside diameter of a loaded sample of the thinnest wall headstamp.
Instructions for honing and lapping dies can be found online, or you can simply drop the die off at a local machine shop with instructions.
Do nothing
While my observation was interesting enough (I think) for an article, I'm not in a hurry to do anything about it - with the possible exception of trading my RCBS sizing die for the Redding. Even without the die change, the .223 ammo I've been loading with my overworked RORG brass is sub-MOA (in other words, it shoots groups less than 2" at 200 yards). I'm not seeing any neck splits either; the normal failure mode for my cases is primer pockets loosening up after a number of reloads. I keep my brass grouped by number of times fired, so even if the sizing die is contributing to excessive work hardening, all of the cases should work harden at the same rate, and the groups shouldn't open up.
It might be interesting to compare the accuracy of rounds sized with a bushing die to those sized (and overworked) with a standard sizing die, but that's a project that will have to go on "The List" for later.