Cartridge Case Longevity (Part 1)
As an instructor, there is one experience in particular that I find truly frustrating:
When I have to reward a really good question with a very bad answer.
For example, when a participant in a reloading class asks, "How many times can a case be reloaded before it must be scrapped?"
The correct (but unhelpful) answer is, "It depends."
A number of factors affect case longevity. The caliber, the pressure to which the rounds are loaded, the firearm used to fire the rounds, the dies used to reload the rounds (and the way the dies are set up), and even the case composition can all have an effect of the number of times a case can be successfully reloaded.
Generally speaking, lower pressures, tighter chambers, better quality components, and dies that are set up to work the case as little as possible all contribute to longer case life. However brass longevity isn't the only thing you have to consider when you are reloading: Some cartridges run best at higher pressures, some firearms have loose chambers, and sometimes you must set up your dies to produce ammo that will run in a number of firearms rather than specifically tailoring it to one chamber.
In order to precisely determine how many times a particular cartridge can be reloaded, you'd almost have to test each caliber/cartridge individually.
So, let's do it. Since we have to start somewhere, I figured I'd begin by testing a middle-of-the-road .38 Special load.
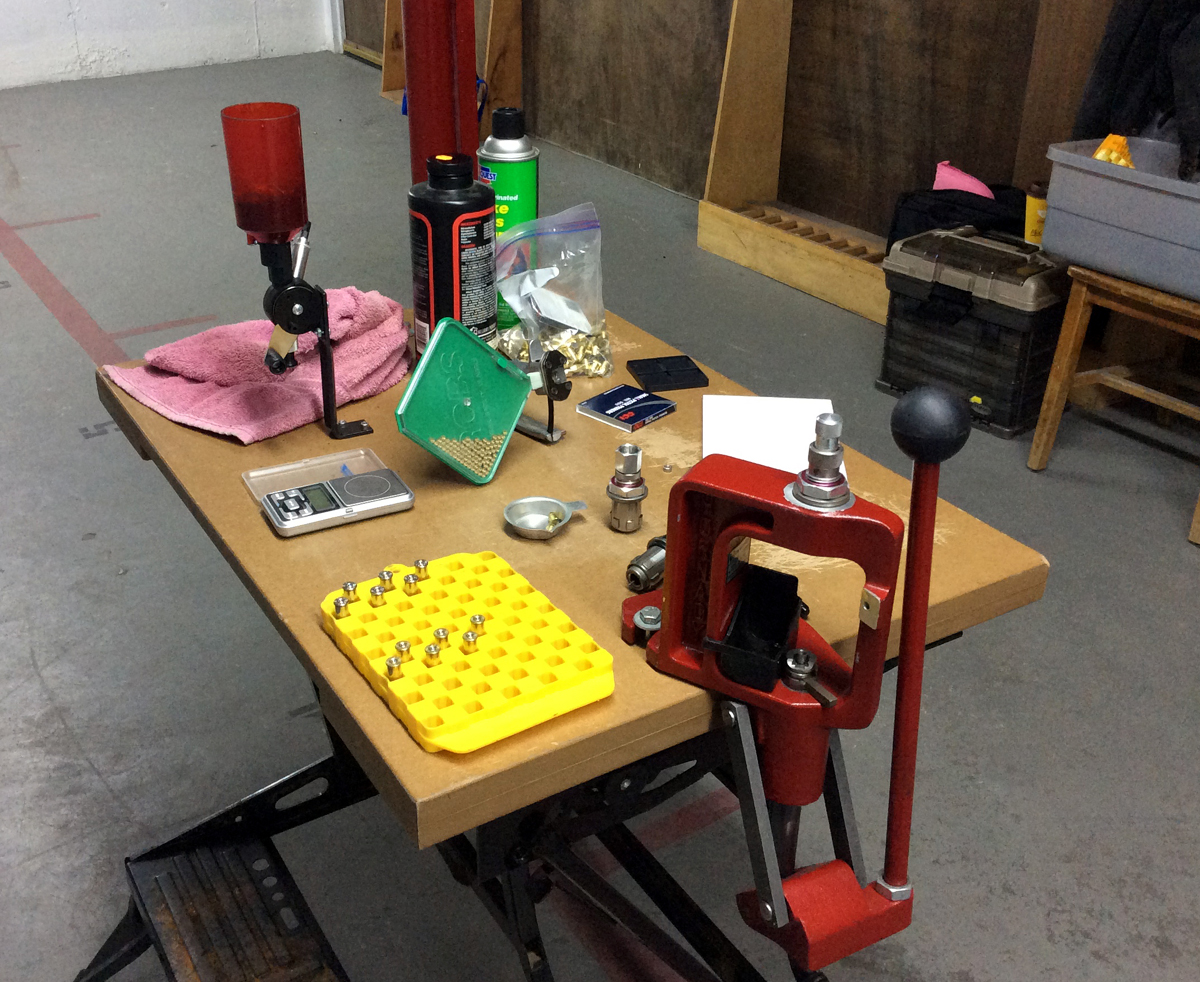
The Test
I brought a portable reloading setup to the range with me (see Figure 1). This setup is similar to the ones I use in the reloading classes.
I loaded the cartridges, shot them, wiped the cases off with a rag, and repeated the process until the cases failed - in other words - until
I couldn't reload them anymore.
For this test, I tried to keep everything as "normal" as possible. What I mean by that is that I tried to use boringly pedestrian data, components, and equipment to load and shoot the rounds in this test. There's nothing exotic here.
I employed a single stage Hornady L-N-L Classic press along with a Lee 3-die carbide pistol die set to load 142gr jacketed bullets over a medium (7.5 grain) charge of Blue Dot for a velocity of about 850 FPS. I flared each case a 'normal' amount before seating the bullets, and finished each round with a light roll crimp. I chose Blue Dot because I had about a quarter of a bottle left over from another project.
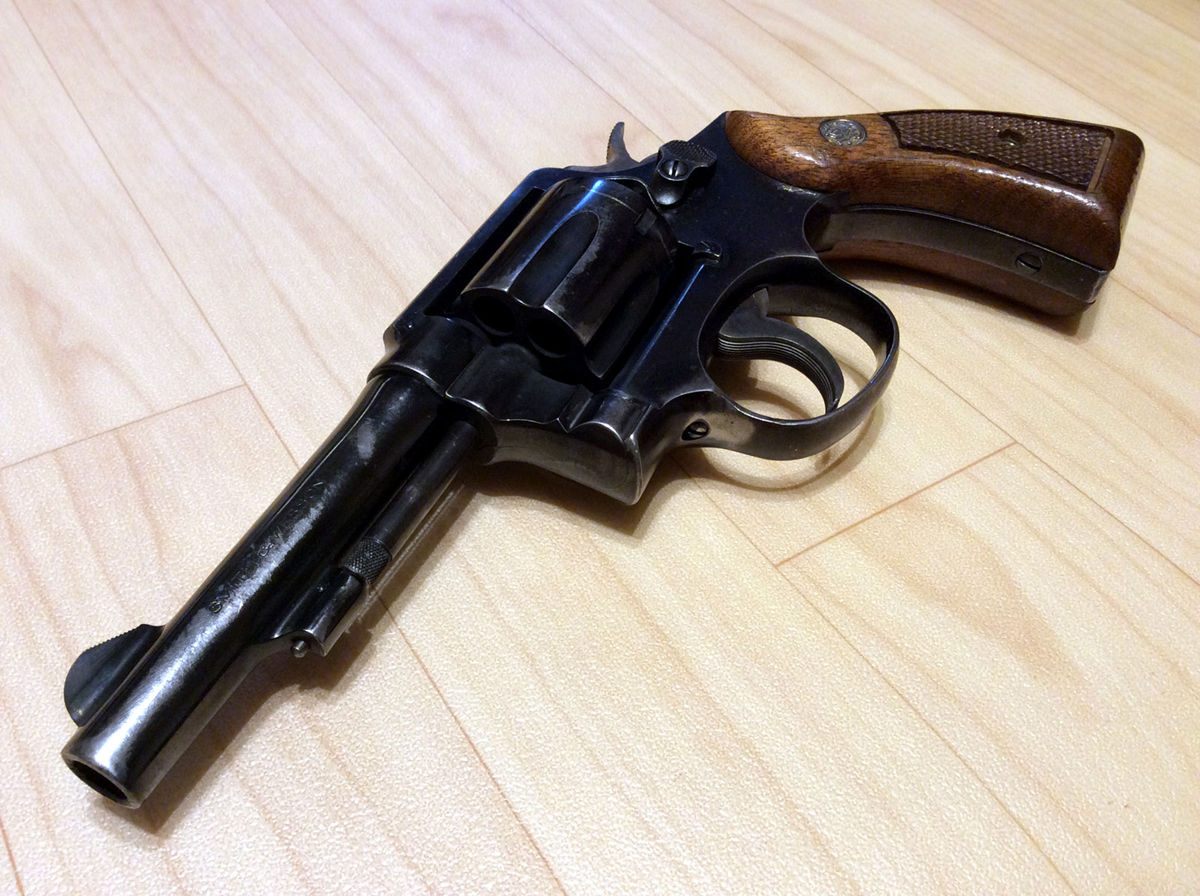
I fired the rounds from a Smith & Wesson pre-Model 10, pencil-barrel, six-shot K-Frame revolver made in the 1950's - when it comes to .38s, that's about as 'standard' as you can get (see Figure 2).
I started with a dozen once-fired Remington (R-P headstamp) .38 Special cases - six were plain brass, and six were nickel plated brass. I used both brass and nickel-plated brass because I wanted to see if one lasted longer than the other. I loaded and shot all 12 cases until they failed.
The Results
The failure mode was the same for every case in the test: the case mouths split (see Figure 3). This makes sense. The .38 Special is a
straight-walled, low pressure revolver round. The primer pockets won't loosen up, there's no case stretch, and the chambers are fairly tight.
That leaves "cracks due to work hardening" as the most likely failure mode, which is exactly what happened to these cases. During loading, the
case mouth is first flared, and then roll-crimped, and then forcibly flattened during firing. It is no surprise that the mouths split because
the mouth ends up getting worked much more than any other part of the case.
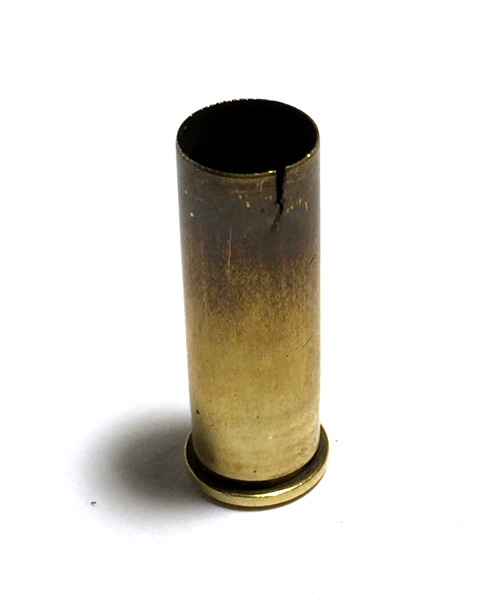
The splits start out tiny - less than 1/16th of an inch long. You can barely see them, but they're easy to feel if you run your fingernail around the case mouth (see figure 4 to see one of the tiny splits). The first couple of times I detected these tiny splits, I tried loading the case one more time. Although the rounds with the tiny splits fired and performed normally, the extracted cases showed significant (about 3/8" long) cracks like the one in Figure 2. After seeing what happened when I loaded cases that were starting to split, I decided to "retire" the remaining cases at the first sign of splitting.
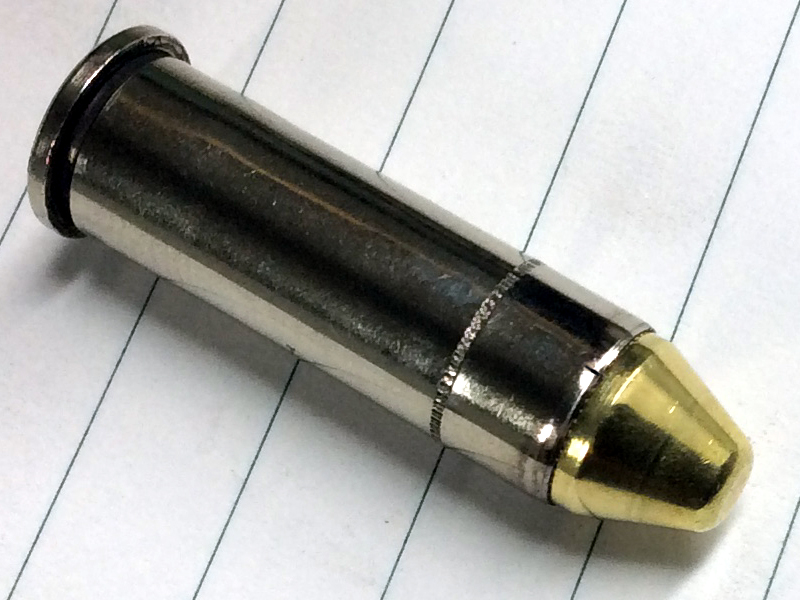
The most remarkable thing I learned during this test was the striking difference in longevity between plain brass and nickel-plated brass cases. I had the feeling going in that nickel-plated cases split sooner than plain brass cases. I didn't realize how much sooner. The plain brass cases lasted 3 times longer than the nickel plated brass. The first nickel-plated case failed on the 6th loading, and by the 15th loading, all six nickel plated cases were split - with an average of 10.5 reloads before failure. The first brass case failed on reload number 28, with one tenacious case hanging on until the 40th reload! The plain brass cases averaged 33 reloads before failure (see Table 1).
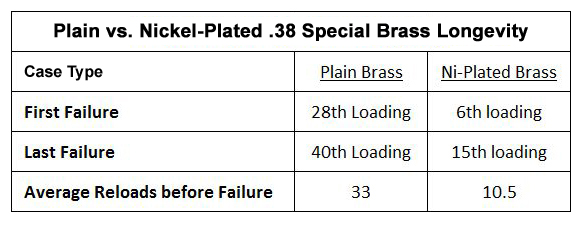
Conclusions
When I take the amount of once-fired range brass I've scrounged through the years, and combine it with the fact that plain brass cases
can be loaded about 30 times, I'm able to conclude that I have enough .38 Special cases to last several lifetimes. I've also decided
that when I buy brass in the future for any caliber, I will opt for plain brass over nickel-plated cases when given the choice.
Since work hardening seems to be the cause of the case failures, it might be interesting sometime in the future to repeat this test using dies that are designed to go easier on the brass. Redding's dual-ring carbide sizing dies work the brass less during sizing, while the new RCBS expander dies and the Lyman "M" expander dies are designed with a stepped expander button to reduce the amount of mouth flare needed for proper bullet seating. Both of these improvements should increase case longevity.
On the other hand, 30 reloads per case is a lot, so repeating this test with different dies to see if I can get a few more reloads per case is probably not going to be a high priority for me.
By the way, the tile of this article says "Part 1" because I intend to test additional calibers in the future. Next up will be .45 ACP.